Imagine the excitement at the starting line of an RC car race. The air is thick with anticipation as drivers make last-minute adjustments to their vehicles. But there’s something different about one car in particular—a sleek, custom-designed machine with parts you’ve never seen before. As the race begins, this unique car quickly takes the lead, hugging the turns with unparalleled precision and accelerating down the straights like a rocket. The secret to its success? 3D-printed parts that have revolutionized its performance.
In recent years, 3D printing has taken the world by storm, offering unprecedented opportunities for customization and innovation across various industries. The world of radio-controlled (RC) cars is no exception. 3D printing is revolutionizing the RC car hobby by providing enthusiasts with unparalleled customization options and performance enhancements that were once only dreamed of.
Benefits of 3D-Printed RC Car Parts
Customization
One of the most significant advantages of 3D printing for RC cars is the ability to create unique, personalized parts that are not available commercially. With 3D printing, hobbyists can modify existing designs or create entirely new ones based on their specific needs and preferences.
For example, a driver may design and print custom bodywork that perfectly fits their car’s chassis, or create a one-of-a-kind spoiler that optimizes downforce for their favorite track. The possibilities for customization are endless, allowing RC enthusiasts to truly make their cars their own.
Performance Enhancement
In addition to customization, 3D printing enables the use of advanced materials and designs that can significantly improve an RC car’s performance. By printing parts with lightweight, high-strength materials like carbon fiber reinforced filaments, drivers can reduce their car’s overall weight without sacrificing durability.
Moreover, 3D printing allows for the creation of complex geometries and optimized designs that would be difficult or impossible to achieve with traditional manufacturing methods. For instance, a 3D-printed chassis with intricate internal structures can provide improved rigidity and weight distribution, while a highly detailed cooling duct can help keep the motor and electronics running at optimal temperatures.
Cost-Effectiveness
Another benefit of 3D printing for RC cars is cost-effectiveness, especially for those who frequently tinker with their vehicles or participate in competitive racing. Rather than purchasing expensive, proprietary parts from manufacturers, hobbyists can print their own components at a fraction of the cost.
Part | Commercial Cost | 3D-Printed Cost | Savings |
Chassis | $100+ | $20 in materials | 80%+ |
Suspension Arms | $30+ | $5 in materials | 83%+ |
Wheel Hubs | $20+ | $3 in materials | 85%+ |
This is particularly advantageous when it comes to rare or discontinued parts. Instead of scouring online marketplaces or paying exorbitant prices for hard-to-find components, RC enthusiasts can simply download a 3D model and print the part themselves.
Accessibility and Community
The increasing accessibility of 3D printing technology has also fostered a thriving online community of RC car enthusiasts who share their designs, knowledge, and experiences. Websites like Thingiverse and Cults3D host vast libraries of free and paid 3D models for RC car parts, allowing hobbyists from around the world to collaborate and build upon each other’s ideas.
This sense of community has accelerated the advancement of 3D printing in the RC car world, as enthusiasts continually push the boundaries of what’s possible with this transformative technology.
Popular Applications of 3D Printing in RC Cars
Hosim Vortan 1:8 Brushless Fast RC Cars
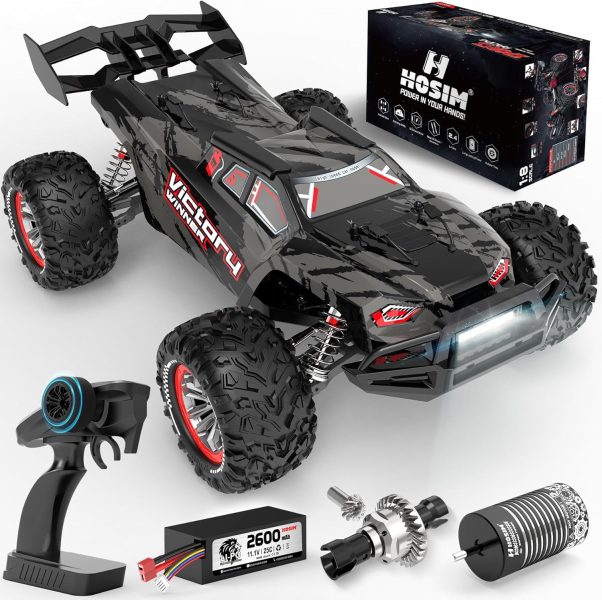
- This remote control car for adults is equipped with powerful 3660 3100KV brushless motor with metal heat sink and metal aluminum center wave box with fan for lightning speed. The built-in 85A brushless ESC gives the RC truck even more potential and upgradability, and is precision engineered for maximum energy conversion. Experience thrilling speeds with our brushless remote monster truck! Compatible with 3S batteries for great upgradability and potential.
Chassis Design and Modification
One of the most popular applications of 3D printing in RC cars is chassis design and modification. By printing their own chassis, hobbyists can experiment with different materials, each with its own unique properties.
Filament | Properties | Applications |
PLA | Easy to print, affordable, biodegradable | Non-structural parts, prototypes |
ABS | Strong, heat-resistant, slightly flexible | Structural components, chassis |
Nylon | Durable, highly flexible, wear-resistant | Gears, suspension parts |
Carbon Fiber | Extremely strong, rigid, lightweight | High-performance parts, chassis |
3D printing also allows for chassis optimization based on specific racing conditions or driving styles. For example, a chassis designed for high-speed drag racing may prioritize aerodynamics and weight reduction, while a chassis built for rock crawling may focus on durability and ground clearance.
Design Tutorial: Custom Chassis in Fusion 360
- Open Fusion 360 and create a new design
- Sketch the basic chassis shape using the rectangle and line tools
- Use the extrude tool to give the chassis depth
- Add mounting points for suspension, motor, and electronics
- Refine the design with fillets and chamfers for strength and printability
- Export the finished design as an STL file for slicing
Suspension and Steering Components
Another area where 3D printing shines is in the creation of custom suspension and steering components. By printing their own suspension arms, shock towers, and steering linkages, RC car enthusiasts can fine-tune their vehicle’s handling and stability to suit their specific needs.
For instance, a driver may design and print a set of front suspension arms with increased caster angle to improve straight-line stability, or create a set of rear shock towers with multiple mounting points to allow for easy ride height adjustments.
3D printing also enables the creation of complex, multi-part assemblies that would be difficult or impossible to manufacture using traditional methods. A prime example is a 3D-printed steering system that incorporates ball joints, tie rods, and servo mounts into a single, integrated unit.
Aerodynamic Enhancements
In the world of RC car racing, aerodynamics can be the difference between victory and defeat. 3D printing has opened up new possibilities for creating custom aerodynamic components that can help drivers gain a competitive edge.
One of the most common 3D-printed aerodynamic enhancements is a custom wing or spoiler. By designing and printing their own wing profiles, RC car enthusiasts can optimize downforce and reduce drag for specific track conditions.
Other popular aerodynamic enhancements include front splitters, rear diffusers, and side skirts. These components work together to manage airflow around the car, improving stability and cornering performance.
Specialized Parts and Accessories
In addition to performance-oriented components, 3D printing also allows for the creation of specialized parts and accessories that can enhance the overall RC car experience.
For example, hobbyists can print custom wheels with unique spoke designs or treads that are optimized for specific racing surfaces. They can also create specialized tire inserts that help maintain the tire’s shape and improve traction.
Other popular 3D-printed accessories include:
- Battery mounts that securely hold LiPo packs in place
- Camera mounts for capturing exciting on-board footage
- Electronics covers that protect receivers, speed controls, and servos from dirt and debris
- Custom tool holders and organizers for pit boxes and workstations
The possibilities for 3D-printed RC car parts and accessories are truly limitless, with new and innovative designs emerging every day.
Quiz: What’s Your 3D-Printed RC Part IQ?
1) What material is best for printing high-strength, lightweight chassis components?
A) PLA. B) ABS. C) Carbon Fiber. D) Nylon
2) True or False: 3D-printed parts are always stronger than commercially available ones.
A) True. B) False
3) What is the most common type of 3D printing used in the RC car hobby?
A) FDM. B) SLA. C) SLS. D) Bioprinting.
1. C, 2. B, 3. A
Materials and Technologies
Filament Types
As mentioned earlier, different filament materials offer unique properties that make them well-suited for specific RC car applications. Here is a detailed comparison of four commonly used filaments in RC car printing:
Filament | Strength | Flexibility | Heat Resistance | Printability |
PLA | ★★ | ★ | ★ | ★★★★★ |
ABS | ★★★ | ★★ | ★★★ | ★★★ |
Nylon | ★★★ | ★★★★ | ★★ | ★★ |
Carbon Fiber | ★★★★★ | ★ | ★★★★ | ★ |
When choosing a filament for a specific part, it’s essential to consider factors like strength, stiffness, heat resistance, and printability. For example, while PLA is easy to print and affordable, it may not be the best choice for a high-stress component like a shock tower. On the other hand, carbon fiber reinforced nylon may provide excellent strength and rigidity, but its higher cost and more challenging printing requirements may make it overkill for a simple cosmetic part.
3D Printing Techniques
In addition to filament choice, the type of 3D printing technology used can also have a significant impact on the quality and performance of RC car parts. The three most common 3D printing techniques used in the hobby are:
- Fused Deposition Modeling (FDM): This is the most widely used method, in which a heated nozzle extrudes molten plastic layer by layer to build up the part. FDM printers are relatively inexpensive and can work with a wide range of materials, making them a popular choice for hobbyists.
- Stereolithography (SLA): SLA printers use a laser to cure and harden liquid resin in a layer-by-layer process. While more expensive than FDM printers, SLA machines can produce parts with extremely high resolution and smooth surface finishes, making them well-suited for detailed components like gears and suspension parts.
- Selective Laser Sintering (SLS): In this method, a laser sinters powdered material (usually nylon) into a solid structure. SLS printers can create strong, durable parts with complex geometries, but their high cost and maintenance requirements make them less common in the RC car hobby.
Comparison: 3D Printing Techniques
Technique | Cost | Resolution | Materials | Ideal For |
FDM | $ | ★★ | PLA, ABS, Nylon, CF | Most parts |
SLA | $$$ | ★★★★★ | Resin | Highly detailed parts |
SLS | $$$$$ | ★★★★ | Nylon, CF | Complex, strong parts |
Each of these technologies has its own advantages and limitations, and the choice ultimately depends on the specific requirements of the part being printed, as well as the hobbyist’s budget and experience level.
Getting Started with 3D Printing for RC Cars
Choosing a 3D Printer
For those looking to get started with 3D printing for their RC cars, the first step is choosing a suitable printer. With so many options on the market, it can be overwhelming to know where to begin.
Printer | Type | Price | Build Volume | Ideal For |
Creality Ender 3 | FDM | $ | 220x220x250mm | Beginners, basic parts |
Prusa Mini | FDM | $$ | 180x180x180mm | Beginners, small parts |
Prusa i3 MK3S+ | FDM | $$$ | 250x210x210mm | Advanced users, most parts |
Elegoo Mars 2 Pro | SLA | $$ | 129x80x160mm | Highly detailed parts |
Formlabs Form 3 | SLA | $$$$ | 145x145x185mm | Professional, high-res parts |
When choosing a printer, it’s important to consider factors like build volume (the maximum size of parts that can be printed), supported materials, print resolution, and ease of use. It’s also a good idea to research the printer’s community and support resources, as having access to a knowledgeable user base can be invaluable when troubleshooting issues or seeking advice.
Software and Design Resources
In addition to a printer, aspiring RC car designers will also need software for creating and preparing 3D models. Some popular options include:
- Tinkercad: A free, web-based platform that offers a simple, intuitive interface for creating and modifying 3D designs. Perfect for beginners.
- Fusion 360: A powerful, professional-grade CAD (computer-aided design) software that offers a wide range of tools for designing, simulating, and rendering 3D models. Free for hobbyists and small businesses.
- Blender: A free, open-source 3D modeling and animation suite that offers advanced tools for creating complex shapes and geometries.
Once a design is complete, it needs to be “sliced” into individual layers for printing. Popular slicing software includes Cura (free) and Simplify3D (paid), both of which offer a wide range of settings and profiles for different printers and materials.
For those looking to get started with 3D printing for their RC cars, there are countless online resources available, including tutorials, forums, and design repositories.
By leveraging these resources and communities, hobbyists can quickly get up to speed on the basics of 3D printing and start designing and printing their own custom RC car parts.
Tips for Successful Printing
While 3D printing offers incredible possibilities for customization and performance, it can also be a bit of a learning curve. Here are some practical tips for achieving high-quality, successful prints:
- Ensure proper bed adhesion: Use a heated bed, apply an adhesive (like glue stick or hairspray), and level the bed properly to prevent warping and ensure that the first layer sticks.
- Calibrate your extruder: Make sure your extruder is extruding the correct amount of plastic by performing a flow rate calibration. This will help ensure accurate, consistent prints.
- Experiment with temperature settings: Different materials have different optimal printing temperatures, so be sure to research and experiment to find the best settings for your specific filament.
Material | Extruder Temp | Bed Temp |
PLA | 190-210°C | 50-60°C |
ABS | 220-250°C | 80-110°C |
Nylon | 240-260°C | 70-100°C |
PETG | 230-250°C | 60-80°C |
- Control layer height: Use smaller layer heights for more detailed prints, but be aware that smaller layers will increase print time. 0.2mm layer height is a good middle ground for most RC car parts.
- Determine the right infill density: Infill density affects the strength and weight of your part. For non-critical components, 20% infill is usually sufficient, while high-stress parts may require 50% or more.
By following these tips and continuously learning and refining their techniques, RC car enthusiasts can unlock the full potential of 3D printing and create truly remarkable custom parts.
Future Trends
Advanced Materials
As 3D printing technology continues to evolve, so too do the materials available for printing. In the coming years, we can expect to see an increasing range of advanced filaments that offer even greater strength, durability, and performance.
Some emerging materials with potential for RC car applications include:
- High-temperature polymers like PEEK and PEI, which can withstand extreme temperatures and stresses
- Metal alloys like stainless steel and titanium, which offer unparalleled strength and rigidity
- Ceramic and composite materials, which combine the properties of multiple substances for enhanced performance
As these materials become more accessible and affordable, RC car enthusiasts will have even more options for creating custom parts that push the boundaries of what’s possible.
AI-Assisted Design
Another exciting development in the world of 3D printing is the integration of artificial intelligence (AI) and machine learning algorithms into the design process. By leveraging AI, designers can optimize their parts for specific performance characteristics, such as weight reduction or strength-to-weight ratio.
AI-powered generative design tools can also explore thousands of potential designs based on a set of input parameters, allowing designers to quickly identify the most promising solutions and iterate on them further.
As these technologies continue to advance, we can expect to see even more innovative and optimized 3D-printed RC car parts that offer unprecedented levels of performance and efficiency.
Bioprinting and Sustainability
Looking further into the future, the emerging field of bioprinting may also have implications for the RC car hobby. Bioprinting involves using 3D printing technology to create structures from living cells and biomaterials.
While still in its early stages, bioprinting has the potential to create eco-friendly, biodegradable RC car parts from renewable resources like algae or plant-based polymers. These materials could offer a sustainable alternative to traditional petroleum-based plastics, reducing the environmental impact of the hobby without sacrificing performance.
Conclusion
3D printing is revolutionizing the world of RC cars, offering hobbyists unprecedented opportunities for customization, performance enhancement, and innovation. By leveraging the power of advanced materials, intelligent design tools, and sustainable manufacturing techniques, the RC car community is poised to reach new heights of creativity and engineering prowess.
As 3D printing technology continues to evolve and become more accessible, it’s clear that its impact on the hobby will only continue to grow. Whether you’re a seasoned racer looking for a competitive edge or a casual enthusiast seeking to personalize your ride, 3D printing offers a world of possibilities limited only by your imagination.
Call to Action: So what are you waiting for? Dive into the exciting world of 3D printing for RC cars and start creating the custom parts of your dreams today!
Share your experiences, designs, and tips in the comments below, and join the vibrant community of RC car enthusiasts pushing the boundaries of what’s possible with 3D printing.
Happy printing, and see you on the track!
Read Other Posts
- The Future of RC Cars: Electric vs. Fuel-Powered Models – An Environmental Perspective
- Optimizing Your RC Car’s Differential for Different Terrains: A Comprehensive Guide
- The Ultimate Guide to RC Car Batteries: Lithium-ion vs. LiPo
- The Ultimate Guide to GPS-Enabled RC Cars: Never Lose Your Vehicle Again!
- RC Car Telemetry Systems Explained: How Advanced Data Boosts Your Racing Performance